Mechanical and Dimensional Calibration
Mechanical and Dimensional
Calibration Services Provided:
- Gage Blocks
- Hardness Tester
- Pin & Plug Gauges, Cylindrical
- Surface Roughness Standards
- Ring Gages, Cylindrical & Threaded
- External Thread Gages (UN/UN STI/Metric)
- Length Standards
- Calipers
- Micrometers (OD & ID)
- Height Gauges
- Depth Gauges
- Indicators (Dial/Digital/Test)
- Snap Gauges
- Feeler (Thickness) Gages
- Tape Measures & Steel Rules
- Precision Levels & Steel Squares
- Protractors & Angle Gages
- Tachometers, Timers & Stopwatches
- Coating Thickness & Thickness Meters
Dimensional Calibration
Dimensional gauges sometimes referred to as “hard gauges” are essential for measuring many different types of components and products manufactured in industries around the world. These important tools are often used in manufacturing processes on a daily basis and their results are depended upon to ensure quality and safety. Due to the frequency of use and demands placed on these tools, it is highly recommended that they be placed on a semi-annual or annual calibration interval.
PCS possesses a growing inventory of highly accurate measuring machines including Pratt & Whitney Labmasters, Universal super-micrometers and a wide range of other of state of the art measuring equipment. Our environmentally controlled laboratories are capable of calibrating gauges with uncertainties of less than 2 micro-inches. PCS is highly capable of efficiently and affordably calibrating your gage blocks, pin gages, plug gauges, ring gauges, and thread plug gauges. In Addition to gage blocks, pins, plugs, rings and threads, we have the capability to calibrate 1-2-3 blocks, ball gauges, length standards, ID micrometers, dial indicators, digital indicators, test indicators, snap gauges, feeler gauges and thickness gauges with the fastest calibration turnaround times in the nation!
Hand Tool Calibration
Superior gauge masters are used to calibrate a wide range of measuring hand tools which are used in almost all manufacturing processes in today’s industry. Gage blocks are a primary part of our procedures for calibrating calipers, micrometers, bore gauges, depth gauges and height gauges. Depending on the size or type of the gauge we may also incorporate caliper masters, micrometer masters, height masters or master length standards to provide calibration points throughout the instrument measuring range. Tape measure and steel rule calibration is achieved by comparison to our NIST traceable master length standards and master steel rules. Precision levels, protractors, angle indicators and steel squares are calibrated in a similar fashon by comparison to master levels, master protractors, gauge blocks and angle blocks.
-
Mechanical Calibration
Our mechanical calibration capabilities are wide ranging and include instruments such as hardness testers, tachometers, coating thickness meters, and many more. One of the most widely used pieces of mechanical testing equipment in today’s industry is the hardness tester. Hardness testing provides critical material performance data and validation. This data helps provide insight into the durability, strength, flexibility and capabilities for a variety of component types from raw materials to prepared specimens and finished goods. Hardness testing is used in a multitude of industries and plays a significant role in structural engineering, aerospace, automotive and medical device manufacturing processes. PCS has the capability to calibrate all types of hardness testers including Rockwell A, B, C, Micro-Hardness (Knoop and Vickers), Superficial and Brinell. Call our team today to schedule your next hardness tester calibration!
Through our vast experience and reputable resources we have successfully added the instruments above to an on-going list of additional calibration services. PCS continuously builds upon its calibration capabilities by researching new ways to apply our multifunctional test equipment to provide a comprehensive solution for your calibration requirements. If you do not see your equipment listed here, please contact us to discuss your specific needs.
PCS is a proud distributor of
,
, and
measuring equipment manufacturers and can help with replacement or new equipment needs.
On-Site Calibration Services
At PCS, we provide on-site calibration services to customers located in Tennessee, Virginia, Alabama and Kentucky. If your facility is near one of the following locations, we can perform your required Dimensional and Mechanical calibration services on-site:
- Knoxville, TN
- Johnson City, TN
- Nashville, TN
- Cookeville, TN
- Bristol, TN
- Murfreesboro, TN
- Kingsport, TN
- Chattanooga, TN
- Abingdon, VA
- Huntsville, AL
- Decatur, AL
- Louisville, KY
- Lexington, KY
Accreditation and Documentation
All calibrations are traceable to the SI through NIST, (National Institute of Standard and Technology) and include “long form” calibration certificates with as-found/as-left data. ISO 17025 accredited calibration is available upon request. We also offer a web based calibration interface, “e-certificates” that gives you access to electronic copies of your calibration certificates which can be viewed and printed at your convenience. Standard turnaround time is 48 hours.
The team at PCS is willing to work hard, when it matters most, to ensure our state crime laboratory system continues to meet stringent ISO accreditation requirements.
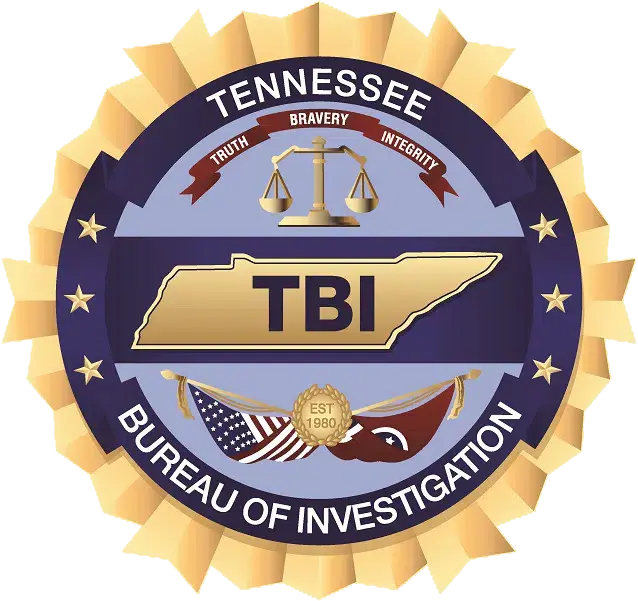
We have been using PCS to calibrate our equipment since 2012. Turnaround time has always been around 24 hrs!!
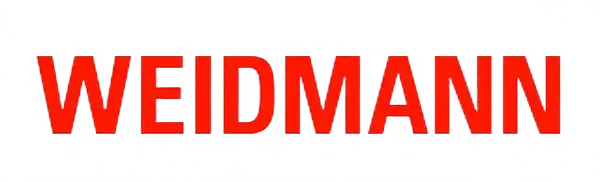
Our CAP auditors, who always inspect us thoroughly, were very impressed with the pipette calibrations performed by PCS.
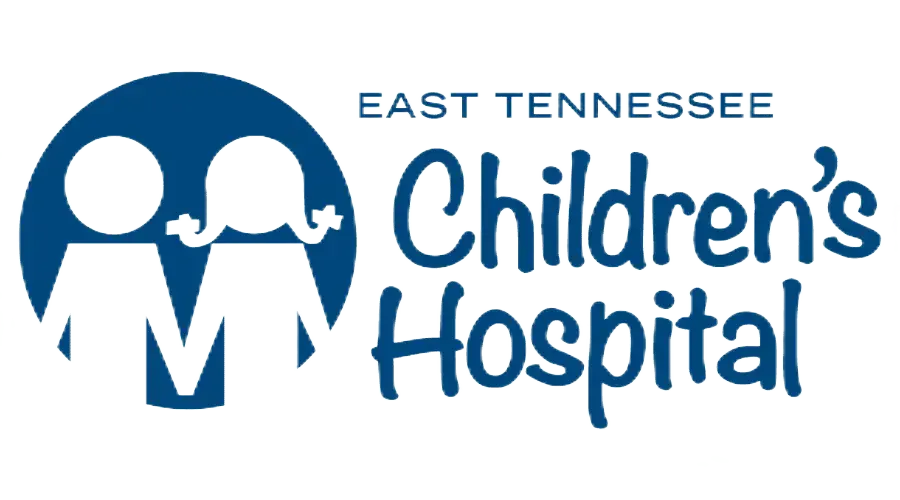
Being partnered with PCS is an absolute pleasure. Turnaround times are always fast and on schedule!
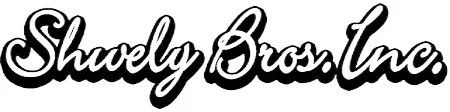
PCS handles a large portion of our outside calibrations. They always provide a quick turnaround for anything we send them.
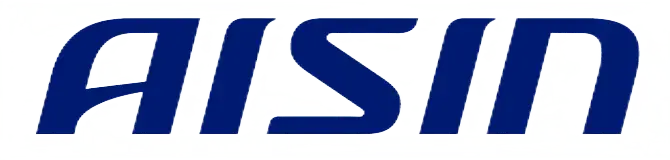
Precision Calibration has provided excellent service for all of our calibration needs and always provide an extremely fast turnaround!

Thanks for the support when issues pop up at our plant. Having calibrated items available at a moments notice prevents a show stopper for customers!
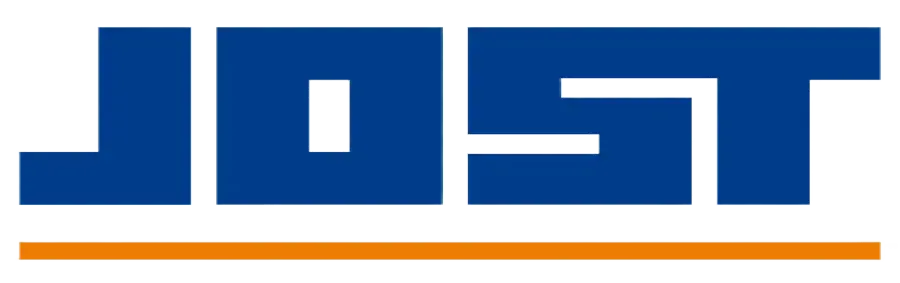
Ready to Send in Your Order?
Office Hours
8am-5pm