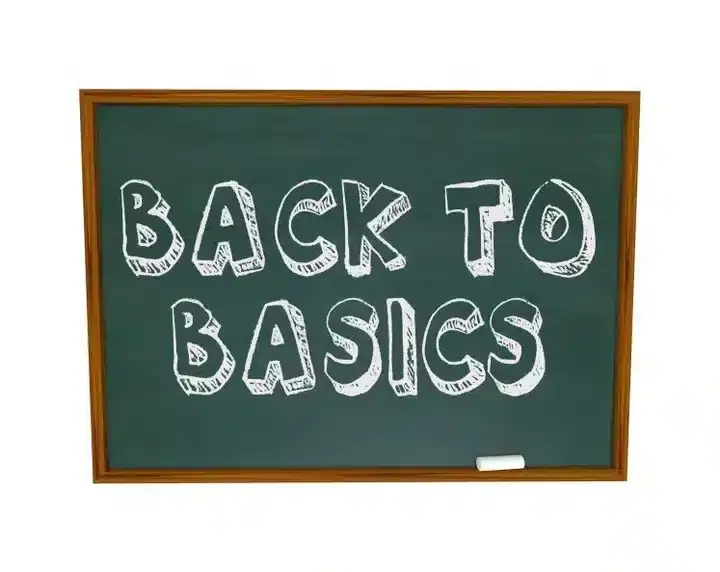
What?
To calibrate something means to check and adjust (if necessary and/or possible) an instrument or piece of equipment to meet the manufacturer’s specifications for inputs and outputs throughout a specified range of use or operation. The process of calibration can help to ensure that a device is performing accurately, predictably, and reliably. Measurements and adjustments are made within certain tolerances which represent very small, acceptable deviations from the equipment’s specified accuracy. Calibration is certified through the process of issuing a report or certificate assuring the end user of a product’s conformance with its specifications. Calibration is carried out by comparing the readings or dimensions of an instrument with those given by a reference standard. Reference instruments are sent out regularly to be calibrated against a recognized national standard.
Why?
Virtually all equipment degrades in some fashion over time. As components age, they lose stability and drift from their published specifications. Even normal handling can adversely affect calibration, and rough handling can throw a piece of equipment completely out of calibration even though it may appear to be okay physically. Regular calibration assures that equipment continually meets the specification required. Having a well-designed and organized calibration program often leads to benefits in quality, productivity, and increased revenue.
When?
Calibration intervals can vary greatly within an industry or plant. Frequency depends on equipment and the application. As a rule, however, calibration should be performed at least once a year. In more critical applications, the frequency will be much greater.
Who?
When planning and implementing a calibration program it is important to use a provider that is qualified and adheres to a national standard. Choosing a company with accreditation to the ISO 17025 standard is the best choice, and in some industries, required. ISO/IEC 17025: 2005 refers specifically to the requirements of testing and calibration laboratories and lays down very rigorous standards for those that use it. Accredited calibration providers, such as Precision Calibration Systems, have oversight protection through their accrediting body with regular audits and reviews, along with very specific Quality Management System requirements. What makes Precision Calibration Systems stand out from the competition is our customer responsiveness and turnaround time.
Reference:
Understanding Instrument Calibration. (2012, December 1). Retrieved July 23, 2015, from https://www.instrumentationtoolbox.com/2012/12/understanding-instrument-calibration.html#axzz3gj5ReJeg
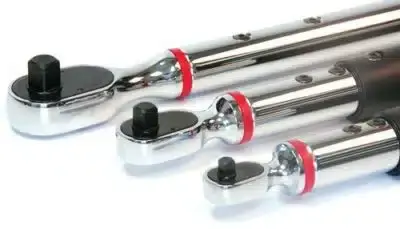
5 Reasons Why Your Torque Wrench Needs to be Calibrated
Whether you’re using a torque wrench in a professional setting or in a home garage, you need to know that your fastener is tightened to a specific...
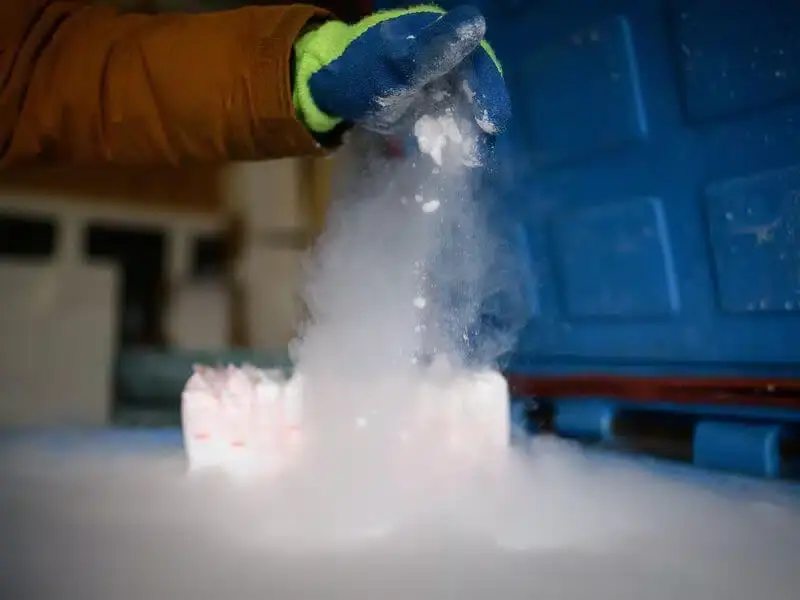
1 min read
Understanding Vaccine Cold Chain Storage Monitoring
With the promise of an effective Covid-19 vaccine on the horizon, healthcare facilities and medical professionals around the country are hard at work...